本项目是两年前进行的,后有诸多原因导致项目终止,虽然没有发射但也积累了诸多经验教训,时值“正反馈”奖励,翻看项目勉强能入眼就发上来了,也借此机会重新规整一下资料,希望对坛友们有所帮助。
开工时没有清晰认识到天上飞的东西结构强度等机械方面的设计不是拍脑袋就能完成的,由此导致的实物工作不理想、实施方案一再调整是项目终止的主要原因,现在看来,本项目的唯一贡献就是在一些工艺和结构上提出并验证了部分设想。
感谢@Orange丶及另一位同学对项目的贡献,部分工作由我们合作完成。
*本作部分工艺与设计没有经过完全验证,借鉴应用前请先验证可行性
*本帖多图
一点新东西:
1、GCC135+GCC137配方RNX真空沉降注射器浇筑工艺
2、3D打印芯模用于RNX药柱制造及脱模
3、3D打印可溶性芯模用于复杂形状环氧基燃料药柱制造的可能性
关键词:RNX;星孔工艺;真空沉降浇筑;3D打印;试车台;推力采集;航电
*********************************正文分割线*************************************
项目需求分析:
笔者在13年曾进行过一段时间的业余火箭活动,最大的感触是大量手工成分带来的不一致性与繁琐操作淡化了一飞冲天的热情。我深知不大可能在业余火箭上倾注太多精力,在缺乏完备理论指导和足够热情的情况下打造“高性能”的火箭是奢望,于是本项目立足于设计制造一种安全可靠、价格适宜、工艺标准化、结构死重小,性能恰好可以用来开展各项验证活动的探空火箭及配套设备。
具体方案选定:
燃料:RNX;真空沉降浇筑;星孔模具
发动机:6061铝管外壳;机加工6061堵头+喷管支架;螺栓固定;耐高温硅胶密封圈;短切玻璃纤维环氧树脂复合喷管;PVC隔热层;铝材与燃烧室隔离
箭体:PVC;手工加工;发动机金属壳体直接外露
航电:STC12主控;预留GY-87模块接口(BMP180气压计/温度计、MPU6050六轴陀螺仪/加速度计、HMC5883L三轴磁场计)可实现气压/姿态/延时开伞;预留NRF24L01 2.4G无线数传+软连接PCB天线;预留GPS模块(面朝天);航电PCB使用分层设计,BTB连接器保障可靠电气连接;搭载高功率蜂鸣器辅助回收;搭载SJ4000运动相机
其余结构:头锥、隔离板、尾翼、大尺寸连接件使用PETG材质3D打印
可以看到在使用的方案中,除了发动机堵头和喷管支架两个部件使用机加工定制,其余结构性部件除箭体外都使用了3D打印直接/间接制造的方法,其中喷管制造尝试了3D打印分体式模具、3D打印阳模硅胶倒模两种工艺,较少且易加工的机加工件大幅减少了成本。
时间隔得比较久,整体的设计思路忘掉了而且这个东西不是像逻辑链一样那么清晰按部就班,不太好描述,总之这枚火箭的设计是各项因素反复拉锯,最后更多妥协于标准件的一个过程。
Part 1 箭体设计:
铁轨的间距会影响运载火箭的直径,那么影响这个探空火箭直径的最大因素是什么呢?答案是水管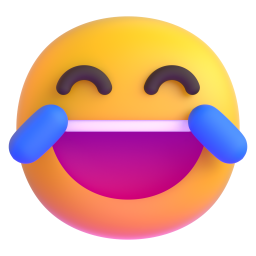
箭体直径不能小到影响航电PCB布局,在满足此前提的情况下,选一个稍细的容易获取的材料作为箭体主要部分,这里使用46*50的PVC水管作为箭体,同样的水管被用于药柱的隔热层。
为了做减重所以决定箭体不套在发动机外面,而是以串联的形式和发动机连接,具体是这样的:发动机堵头一侧有两排螺孔,一排用于连接堵头,一排用于连接箭体,箭体有一部分没入发动机壳体中,连接处内部放置一个固定件,用于装载螺母完成对箭体的锁定,同时起到隔离可能泄露的燃气、保持箭体连接不偏心的作用。
事实证明这是个不太成功的设计,首先这种串接的方式仍会出现小幅度的偏心,其次缺乏隔热设计,发动机在20秒的非正常工作后(设计5S内),连接处温度达到了80摄氏度,此温度会软化连接处的PVC,当然正常工作的温度会低于此。
箭体分为伞仓和航电仓两截,两者之间用打印件挡板隔离,打印件挡板伞仓一侧有一打印件燃气活塞,挡板与燃气活塞之间留有点火头和药室,点火头由航电直接驱动。
航电仓在运动相机镜头的位置有一开口,相机的镜头直径大约35mm,对气动的影响未知。
显然这个箭体可用速度不高。
Part 2 发动机设计:
关于发动机,一开始为了项目进度选用KC3025套件做发动机,无奈求购无货,于是开始了自己的坑爹设计,喷管堵头均主要参考KC3025,实际上可以兼容。
发动机的直径和箭体接近,与箭体相同的PVC管用于发动机内隔热层,壳体选用内径50mm的 6061铝合金管。
鉴于铝合金材料难以加工螺纹且螺纹连接方式工作后难以拆卸的劣迹,在此使用螺栓连接,此方案下壳体加工较为方便。
喷管方案比较纠结,设计了45#钢喷管,发现重量感人且加工麻烦,考虑到机加工件通用的可能(改变药柱长度不需重新加工),并且看到了一些文献使用环氧树脂和玻纤混合达到了不错的抗热和机械性能,心里长草决定使用机加工件喷管支架+玻纤环氧喷管的方案(事实证明非专业情况下的 照论文和泥 照葫芦画瓢是个大坑),将喷管重量从45#钢的288g缩到16.5+42.5g,加工费用也有所降低。
鉴于制造方便原料易得,燃料定为RNX,发动机内装150mm药柱*2,取隔热层内层面积为最大燃烧面积,则为500cm^2,燃料质量为732g,比冲取90s,总冲645N*s。
原计划:设计中取喷燃比为600,压力约5Mpa,可知喷喉直径为10.2mm。
后由于RNX配方变更为GCC135+GCC137,燃料特性变化,修改喷燃比为950,压力约4.1Mpa,喷喉直径8mm。
取喷管扩张比为12(参考KC3025),取扩张半角16度。
壳体耐压方面,50*54 6061铝合金管,安全系数1.5情况下可耐压14Mpa,实际使用是50*55的管,耐压余量比较充足。
喷管支架与堵头均使用12颗12.9级M4螺栓与壳体连接,安全系数2的情况下耐5Mpa内压,此处螺栓连接设计实际工作效果存疑,铝壳体能否承受剪切力还不得知。
50mm密封圈截面积3.14mm^2 应设置2mm宽,1.5mm深密封槽 ,密封槽在堵头和喷管支架上各加工一圈。
堵头参考了KC3025的设计,中心孔换成M20*1.5螺纹方便直接安装压力传感器或塞入点火药,若不使用则用机米螺丝封死。
之所以说这个发动机的金属部分是和热流完全隔离的,体现在:燃料棒侧面隔热层 ;堵头端面环氧粘合 ;喷管与燃料棒粘合 ;喷管材料绝热性好 几个方面。
Part 3 简单气动设计:
这里所谓气动设计,就是把设计好的箭体、发动机、其它部件尺寸质量等信息放进去,看看头锥需要配多重、尾翼需要怎么设计才能保障较高的稳定系数,此处稳定系数为1.44
气动设计依靠Openrocket完成,感谢坛友对软件的汉化,让我除了挠头以外有其它手段来进行气动设计
发动机那块参数选了一个稍微接近比较保守的,理想情况速度还是挺快的。
此处头锥取100mm露出长度,为箭体直径的两倍,萌新不太懂头锥曲线怎么办,直接找冯卡门曲线代入了一下画了外形,保障3mm以上的壁厚,用PETG打印之,打印出来还是质量很好非常光滑的,不过PETG耐温只有70度,估计实际在亚音速下撑不住。
尾翼是六片四边形后掠翼,六片是因为PETG打印件翼展过大不够结实,只能降低翼展增加翼片数量,没错尾翼是打印的...和拉喷整流罩一起固定在发动机尾部,事实再次证明这种设计没有做金属和打印件之间的隔热处理是不行的,试车中喷管附近特意放置了同样的材料用于测试,结果熔化地非常彻底,当然这和发动机长时间燃烧有关。
关于打印件的强度问题,PETG本身具有相当好的韧性(相对于其它廉价打印材料来说),在打印时精调切片软件使得翼片由四条或者更多0.4mm熔丝紧密贴合而成,基本形成一块整体,实测将其弯折30度左右仍能恢复,强度比同厚度木材要好。在另一个项目的例子中,较大面积PETG打印薄片作为固定翼蒙皮表现得比较耐操。
对于FDM做气动部件,个人认为解决温度问题后是有一定可行性的...
Part 4 航电系统设计 :
作为学电的,我觉得这里的航电没什么好说的...当前无非是把四轴上的那些传感器塞到火箭里,考虑一下抗震啥的..
航电的板子是刚学PCB没多久画的,布局乱的一比,芯片选型和晶振啥的放在火箭上不太合适
四块板:分别为电源、主控、传感器/通讯、GPS
板间供电使用铜柱,信号口使用板间连接器KF141,点火头等外部设备接口使用SM-4P接头,分离力400N,使用两种特殊的接口是为了提高在高震动下的可靠性,参考了论坛前辈的经验
除了四块板还有锂电池、高音蜂鸣器、运动相机被整合在一个圆柱体框架内。
航电系统如果完全按照设计的话,可实现这些功能:
·无线传输,与地面站远程通讯、接受遥控
·采集分析气压、温度、加速度、角速度、地磁场,在指定情况下控制开伞,用的都是烂大街低端传感器
·直接连接点火头 程控点火开伞
·接收GPS信号并记录
·控制运动相机开始录像(快门键被引出)
·驱动蜂鸣器发出刺耳的尖啸
电路设计没啥问题,这个可靠性我还是有信心的
,可是发动机不过关做好航电干什么呢..
Part 5 燃料棒制造工艺:
燃料棒的制造耗费了相当大的精力,使用3D打印芯模的方法成功进行了制造,验证了3D打印可溶性芯模的可行性。
制造燃料棒需要的设备有:真空仓(自制);超大注射器(鼻饲用);震动座;加热装置(可选)
具体制造过程:
1、制造氧化剂粉并充分干燥,干燥不充分会导致成品燃料棒品质不佳,燃烧慢残渣多
2、芯模充分涂抹脱模剂,芯模与隔热层安装结合,接缝处临时封死(热熔胶之类),安装震动座,放入真空仓
3、将氧化剂粉末与树脂称重混合,将药泥均匀混合
4、药泥装入注射器,注射器塞入胶塞,与真空仓形成密闭环境
5、开真空仓,对注射器出口附近进行预热以加强流动性,间歇性启动震动座
·此过程持续进行,可见药泥像挤牙膏一样被连续吸出,药泥脱离注射器后由于内部气泡膨胀而爆裂,落入隔热层-芯模形成的容器中,开启震动后迅速流平
·未浇筑药泥较多时,注射器芯杆可不加,直接向敞开的注射器中添加药泥,流动的药泥会密封整个环境,药泥较少时会出现“塌陷”,出现一个孔洞使得真空仓直接与外界联通,破坏真空
·若浇筑时间较长,可对芯杆手动加压来加快注射,燃料可分批混合并添加,一次性加入过多量的药泥会提前固化,降低流动性
·浇筑过程建议两人配合,节奏需把握
6、浇筑完成,取出隔热层-芯模-药泥结合体,等待部分固化(药泥有较好硬度且保留一定弹性),对药柱及芯模进行加热,拔出芯模
·RNX完全固化后再拔出芯模难度很大,对取出芯模的时间把握非常重要,过早尝试拔出会破坏药柱形状,我们在涂抹脱模剂的环节中涂覆了一定厚度的凡士林,对这个过程能起到比较好的帮助作用。
·芯模表面的平整或是添加倒角有利于顺利取出
7、等待完全固化后切削端面,修整隔热层厚度,完成制造
俯视真空仓内,HIPS材质芯模与其定心支架被固定在隔热层中,隔热层外面是震动弹性组件,偏心电机在下部
关于内孔形状:
内孔为zzlzhang发过的七角星孔,适配50mm直径燃料棒,燃烧时能保持几乎相同的燃烧面积(与隔热层内面积接近)
重传一次
七角星孔平面图.dwg
33.26KB
DWG
89次下载
关于可溶性芯模:
基于脱模过程中的一些烦恼经历,认为脱模过程有过多不可控因素,于是尝试一次性的可溶解芯模,其相较于传统复用模具,可进行非等径、复杂形状的内孔制造。
首先尝试的是HIPS+柠檬烯溶剂,然而并不能溶解,泡了几天HIPS只是软化,或许是HIPS打印耗材里加了什么东西,费力刮去软化部分后变成了这样,这部分燃料被用于第二次试车,燃烧不太好
之后隔了一段时间尝试了PVA水溶性材料,意外地很容易打印,另外测试了把一块RNX切片泡到水里一天再晒干,点燃正常,残渣很少,说明PVA溶解过程不会对RNX燃料棒产生不可逆影响
理论上来说PVA被用来造药柱只差一步了,可是此时项目已经凉了,材料设备凑不齐,有其他事要忙,只得作罢
可溶性芯模设计是空心的,用以加速溶解,减少耗材,制造这样一个PVA芯棒耗材20g
、
从干燥箱里取出放置了一年半的PVA一次性芯棒,色香味甜入口即化
如尝试水溶性芯棒方案,请注意PVA耗材从拆开包装后就需放在干燥箱中,且需于干燥时打印
Part 6 不成功的复合材料喷管:
起初看到了这样的文献,感觉可以一试
玻璃纤维增强环氧树脂复合材料的力学性能研究.pdf
836.77KB
PDF
185次下载
预览
喷管制造材料为:E44+T31树脂 质量80% 6mm短切玻璃纤维(浸润剂处理后) 质量20%
然而玻璃纤维像棉花一样松散,与树脂混合简直是灾难,树脂较粘稠,不容易渗透到纤维内部
于是把混合物装到自封袋里,反复揉捏,得到一坨很粘的黄色胶状物,塞入涂了脱模剂的模具
模具一开始是这样的,比较酷炫
脱模中:
可以看到存在大气泡,这个操作难以放入真空仓进行,混合物过于粘稠,如果能真空操作的话对提高质量有很大帮助
由于喷管形状复杂,硬质模具难以将药泥压入进行操作,后又尝试了硅胶模具
先精调尺寸,打印阳模(不懂如何称呼,就是和目标零件一模一样的模具),浸入硅胶,硅胶固化后取出阳模,然后倒入树脂混合物
这样的方法相较于硬模好操作一些,但工艺效果仍然不理想
在试车测试中,这种喷管在发动机非正常工作二十多秒的摧残下,喷喉处从10mm被扩至16mm ,若发动机正常工作(3S),情况会好转一些。
烧蚀对比图,可见被烧蚀严重
截至目前的测试,可知此种喷管在抗烧蚀性上表现不理想,抗压性能未知(在设计时取纯环氧的机械性能带入计算)
具体制造操作时没有严格按照论文中的环境,只是保障了配方大致正确,这样照葫芦画瓢是不正确的,鉴于我的手残操作,这种材料真实性能不一定不能用于喷管
一些设想:
·航天用复合材料喷管制造工艺过于复杂,若能寻找一种类似于RNX、APCP的材料配方,用制造这些药柱的类似工艺制造喷管(混料-药泥-入模-固化),或许可替代金属喷管
·在此方案中喷喉处加入石墨环以防扩孔
Part 7 辅助&测试设备:
主要介绍:真空仓、试车台
真空仓:
对于真空仓我非常满意,好用好看还便宜
设计最大可制造50mm直径,长度200mm药柱
真空泵使用某宝名为VN-T1的小泵,负压最高-85Kpa,项目前期多处搜集信息后判定此真空度够用,实际使用中达到-80Kpa
蒸汽风格,特殊的美感
真空仓结构如图,包含真空泵、电源盒、水管、泄压旋钮、真空表、仓体、仓盖
泵使用12V供电,两个拨动开关除用于控制泵外还控制接入仓内的一个T插接口,可用于照明/震动电机/加热
泄压旋钮可以手动控制放气,不然想打开仓盖要费时间
真空表型号是Y-60啥的
仓体是110mm水管,一边端盖挖空,粘上亚克力板用于观察,亚克力板有一小口用于安装胶塞。
非活动部分全部树脂封死,活动部分使用凡士林密封
试车台:
试车台使用20mm铝型材搭建,传感器量程100kg
使用HX711模块(按论坛教程改动以提高采样频率),捡了个51开发板采集数据,串口发送到笔记本上
竖着放的试车台,形似发射塔
图中的发动机固定方式是不正确的,仅用打印件对发动机作径向约束很不安全,后续设计已经改进
通过站到测量平台上的方式对试车台稳固性进行验收测试...
实际安装示意,试车台背靠大石
***********************************************************************************************
总结及反思:
·一个完整的业余火箭工程从设计到制造牵扯很多方面,设备材料多如牛毛,相较于其它科技爱好关联学科更多、实施难度更大
·想追求“一飞冲天,直上九霄”的情怀,没有扎实功底往往落得一地鸡毛,真只想上天一爽,不如买个商品发动机,精力放在其它部分
·做项目有时不能钻牛角尖而忘记整体目标,用现成的经常比自己凑合出来的要靠谱
·设计阶段能考虑到的,尽量考虑,做到一半发现不行很麻烦
自此项目后,不再想“手工打造”什么作品,目前动手仅限于拧螺丝焊元件,SLS金属打印普及后或许再战火箭
200字以内,仅用于支线交流,主线讨论请采用回复功能。